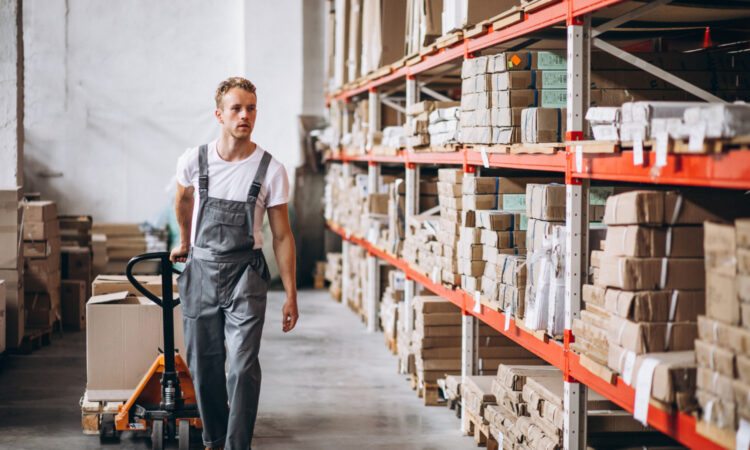
There is a classic saying in warehousing that says, “If there’s available area, somebody will eventually fill it, ” often at some point. For that reason, it isn’t unusual for a warehouse is complete even during slow durations.
A warehouse will usually come to an end of area considering rapid growth, regular peaks, huge rebate purchasing, planned stock builds for manufacturing shutdowns, center combination, as well as a sluggish sales duration.
Generally there are three forms of space inadequacies that take place in a warehouse. The very first kind results from simply having an excessive amount of suitable inventory. The second reason is the result of having too much of the wrong merchandise, and also the 3rd arises from utilizing the present warehouse area defectively. To properly deal with these space dilemmas, you have to first comprehend the issues and exactly what creates them.
Too Much of suitable Product
A good amount of the best product appears positive in terms of customer support and order fulfillment goals, as item is readily available to fill client requests. However, as product sales staff and buyers celebrate making consumers happy by fulfilling every order 100percent, the warehouse runs really below set up output and safety standards. A look into this particular warehouse will unveil pallets of item stored in aisles, stacked in dock places, put on rack end caps, or multiple SKUs of product combined in solitary bin areas. Obstructed visibility produces security hazards, insufficient simplicity in finding inventory, diminished work output and multiple handlings of item. The upside usually the products often move quickly through the warehouse and space issues exist just for weeks.
Too Much of not the right Product
Having an excessive amount of the incorrect product is generally an indicator that product sales forecasts and/or production preparation were incorrect, but inaddition it regularly shows the warehouse is certainly not handling stock levels or outdated item properly. Unlike having too much of the best item, where inventory peaks are handled with additional labor, having the wrong product usually results in inventory remaining untouched in the warehouse for months and even years.