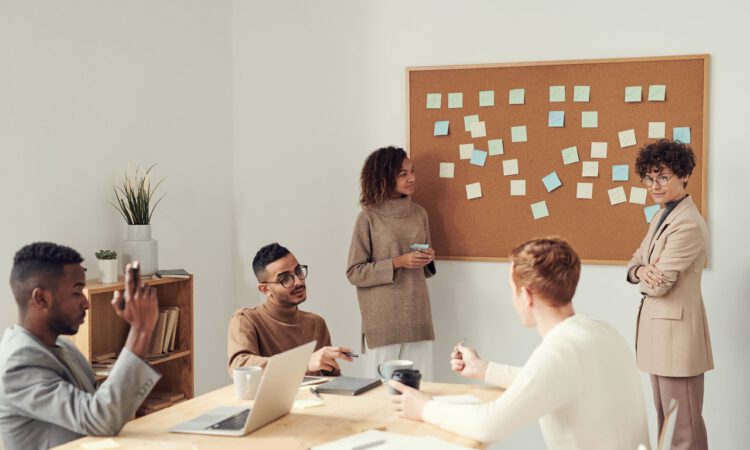
Businesses frequently think their choosing procedure is efficient providing services and products roll out on time and clients are happy. But the majority selecting operations in warehouses across The united states could use a reorganization, and it’s exactly about the method, you understand … and instruction, and folks, and methods!
The following are 10 tips to increase warehouse procedure:
1. Profile your orders.
Your most well known SKUs likely change aided by the months, therefore re-slot your warehouse to allow for your business model, and review the setup at least once per year. This means that your “A” SKUs are in the appropriate storage space news and real location, reducing unneeded travel for your order pickers. Your warehouse administration system (WMS) need to have a dynamic “slotting” component.
2. Assess your overall selecting methodology.
Ensure that your selecting methodology matches your company. Whether you select single purchase, multi-order, group choosing with a single picker, or area selecting, the best picking methodology is critical for optimizing efficiency. Hey, you can always ask a 3PL to evaluate it!
3. Utilize software to sequence sales.
Sequencing your instructions by choose road, and batching collectively solitary lines, same-zone requests, and hard selections – such non-conveyable items – saves great time regarding distribution center flooring. Once more, your WMS computer software can arrange the workflow and optimize sequence performance.
4. Create a warehouse within a warehouse.
In the one-hand, you’ll get tremendous efficiency by grouping together the 20 per cent of SKUs that total 80 % of one’s orders. This slices travel time for your pickers. Be sure, but that 80-20 area or area is properly designed to accommodate high-volume activity.
However, this will be sort of traditional reasoning; inside day and age of the Long Tail, may very well not have the ability to utilize 80-20 rule since you are attempting to sell “few of numerous, ” as opposed to “many of the couple of!”
5. Examine your storage equipment assuring appropriate application.
Putting slow-moving, low-cube products in container shelving and fast-moving things in carton/pallet movement – or other proper storage space options – improves storage thickness and picker efficiency. This lets you much better utilize the DC’s cube. Seasonal as well as other campaigns can wreak havoc on this notion, therefore beware.
6. Create “wheelhouse” zones in your choosing location.
It is possible to increase selecting efficiency and enhance order picker ergonomics by slotting your fastest-moving SKUs into the waist-to-shoulder or “wheelhouse” part of your storage space media.
7. Designate just two or three standard shipping cartons.
With just two or three cardboard boxes available – plus some customized sizes, if required – pickers will put instructions together faster. Reducing sizes optimizes cargo expenses and lowers corrugated invest. In addition makes it much simpler to guide a pick-path methodology.
8. Start thinking about automation.
Order pickers invest about 60 per cent of their own time walking item or moving item around. Start thinking about an automated answer, such as for instance conveyance, to cut back their considerable travel time. Multi-level pick towers in addition save travel time and are very revolutionary.
9. Understand your technology options.
Many choices are accessible to increase efficiency – including bar codes, radio frequency, pick-to-label, pick-to-light, and voice-activated technologies. These technologies are created to provide various amounts of increased selecting productivity and improved precision.