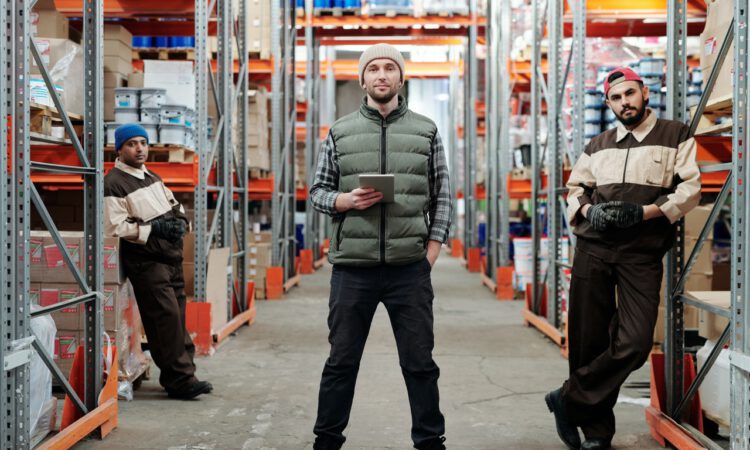
Efficient management of inventory is very important to an organization’s important thing. For example, it costs money to keep inventory, so inventory supervisors you will need to determine the minimum level of warehouse room necessary to shop the absolute most of stock necessary for the company’s continuous production needs.
The stock turnover proportion is among the key metrics managers used to determine whether or otherwise not they actually do a good task managing their particular inventories. Generally speaking, the higher this ratio is, the better it really is for company, because it implies inventory just isn’t sitting idle on shelves, but instead is being used in production or being sold in shops.
In the end, inventory management varies according to precise product sales predictions. Technical advances in inventory systems and computer software have allowed organizations to handle their particular inventories at an extremely efficient degree predicated on those forecasts, and have led to the popularity of just-in-time stock administration. In fact, some companies, like Dell Computers, are becoming therefore sophisticated due to their inventory administration that they don’t order the recycleables to manufacture a finished product until a person puts an order.