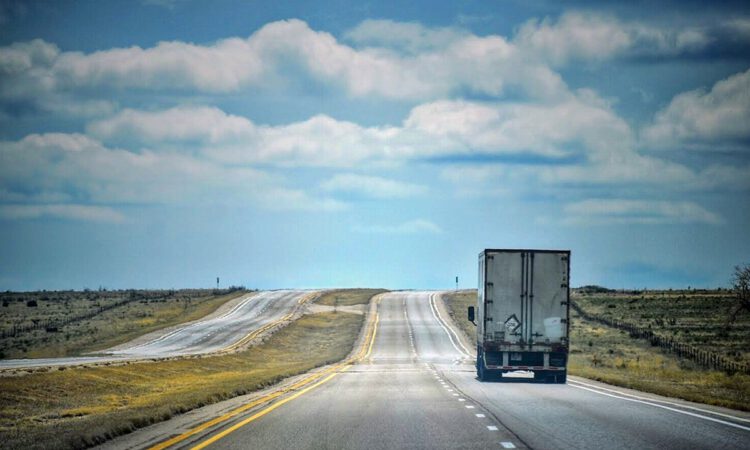
Businesses tend to be trapped in a constant pattern that pushes them to improve their company to get a competitive advantage. They consistently have the tension to cut back expenses, time and inventory. A good way that features which may improve an organization substantially is a supply sequence procedure generally Lean Logistics.
What is the significance of Lean Logistics?
Slim Logistics, in other words, can be described as an approach to recognize and get rid of wasteful tasks from supply chain to be able to increase product circulation and rate. In order to achieve Leaner Logistics; companies need to apply leaner reasoning. Companies that include lean thinking to their supply sequence will benefit from enhanced customer service, paid off environmental influence by lowering waste plus total corporate citizenship.
What is Lean Thinking?
Lean Thinking originated from production practices used by Japanese automotive producers. Because of minimal resources and shortages, they employed a production procedure that worked with minimum waste. This thinking quickly distribute to any or all manufacturing places, new product development and supply string administration. (Krafcik and MacDuffie, 1989)
Slim Thinking involves a consistent pattern of pursuing perfection by detatching waste and maximizing product value. This technique means end-customers don’t purchase company inefficiency and waste. Four principles take part in achieving minimal waste:
- Specify price: Consumer value is identified and added over the offer sequence community.
- Map out worth flow: distinguishing all procedures across the supply sequence network to be able to eradicate the processes that do not develop value to your total product. This mapping allows us to understand how the worthiness is established in to the item from the customer’s viewpoint.
- Create an item circulation: Applying the elements outlined in order to make valuable processes to occur in a smooth system; minimizing interruptions, stocks, downtime.
- Establish customer pull: production just in response through the buyer more will become necessary; implying that need info is provided over the supply chain.
Each of these four procedures seeks excellence to increasingly enhance every procedure; reducing waste and maximizing value.