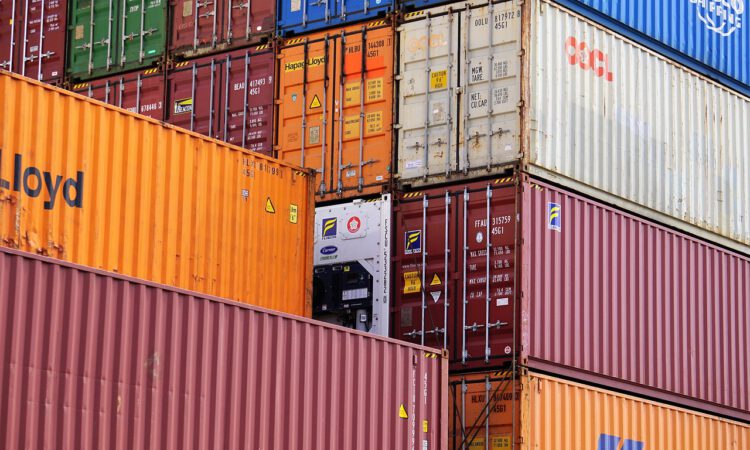
Efficiency and reliability will be the cornerstones of smooth functionality for a warehouse. By standardizing item storage space and packaging processes, your small business can lessen unneeded traffic and help prevent shipping errors. By conducting a yearly breakdown of shipments and regular trends, your organization make crucial staffing and purchasing corrections to maximize productivity. Listed here are ten tips designed to help to improve your online business by optimizing the performance of your warehouse operations:
1. Designate a place of one’s warehouse given that storage area for tiny parts and add-ons.
By isolating items such components and consumables in a protected location with appropriate storage space pots, warehouse managers enables avoid the loss in smaller pieces. Sometimes, it could be beneficial to have a supervisor oversee this area of the warehouse.
2. Put older inventory things at the front of rack to ensure that they ship initially.
This might be specially essential for small businesses that offer items with a conclusion date or even for those businesses that resell services and products bought with a time-sensitive factory warranty.
3. Designate two or three areas as “easy accessibility” areas of your warehouse.
Warehouse selecting staff must have comfortable access to the items that are requested using best regularity. These places don’t have to take to much room, especially if you make use of some smart business strategies in their creation. An expert from suggests making use of stackable storage space bins to increase the actual quantity of space for storing readily available.
4. Shop heavier and slower-moving products over the top amount racks or in right back of center.
Regions of the warehouse which are not an easy task to achieve or accessibility is reserved for slower moving services and products or those things that need a forklift to move.
5. Standardize your packaging process by making use of just 3 to 5 various size containers.
Besides increasing the efficiency of one’s packaging staff, restricting the amount of box and crate dimensions that you keep on hand wil dramatically reduce packaging and delivery costs.
6. Make sure the packaging area is located as near to the running dock as you can.
This reduces staff traffic and stops packaged things from becoming lost or damaged before they have been transported.
7. Set-up the quality control “QC” area as close as you possibly can into the packaging location.
The QC process need is the final and a lot of important stage associated with purchase preparation process. It really is crucial that things remain clear of contamination or unneeded managing before they truly are packed. As soon as the QC place is right beside the packaging location, the likelihood of contamination is greatly decreased.
8. Conduct an annual post on your order totals for every single item.
By knowing which items are more and minimum popular, the warehouse manager can coordinate with purchasing staff to suggest feasible adjustments to purchasing cycles.
9. Think about shipping patterns and top times when designing staffing schedules.
Manufacturing bottlenecks could be avoided by anticipating maximum manufacturing times and increasing staff during those cycles.