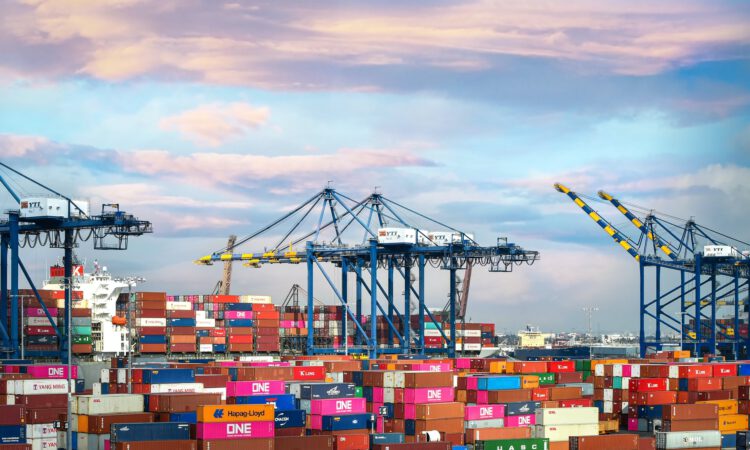
Companies invest any quantity of dollars required – on anything from study & development, to product installation, to packaging and delivery – to get a brand new product out and ready for its customers, whether it is on the market via offline, e-commerce or both. While a company’s forward logistics operations may be sturdy and high in detail about getting a brand new product into a customer’s fingers, it does not necessarily mean that their particular reverse logistics practices tend to be as completely developed.
No company desires to believe that their products will begin to become back their hands after a-sale, but having a foolproof reverse logistics process set up could be the online game changer that sets one business aside from its competitors – particularly when considering examining that bottom line. Below are a few typical reverse logistics problems that lots of businesses end up in, and some suggestions about how your company can prevent them:
Map Out Your Reverse Logistics Warehouse
That one may seem like a good investment, but neglecting to correctly plan for your organization’s reverse logistics warehouse needs could show to be a very problematic move. Many companies think that having a designated destination to store comes back is all you’ll need – which is far from the truth.
Your warehouse is mapped off to integrate details eg in which the product goes because goes into the warehouse, where the information capture occurs, in which it can be disassembled and reassembled, or where in actuality the unused elements could be recycled.
Also, the returned products should be kept far away from the assembly of brand new products to eliminate any chance of a defective component making its way into some new packaging.
Contain The Expenses
A highly effective reverse logistics procedure is just one that may open up additional streams of revenue for a company – not just one that consistently produce unnecessary expenditures – which may occur if a suitable price containment system is certainly not implemented.
Easy things such as a growth in problems for one item element or running out of a crucial little bit of packaging for refurbished products could be the hushed triggers that deliver your reverse logistics system haywire. This could quickly snowball into a scenario in which you’re racking up additional prices that go beyond the profit gained by putting the refurbished product straight back on the market originally.
Information Knowledge Is Secret
Managing your comes back and having a simple yet effective return process begins with information understanding. It’s exceptionally important for know precisely how much product is coming as well as what their dilemmas tend to be.
Getting the appropriate information capture practices and keeping track of methods in place could be the distinction between building a reverse logistics procedure that gets better your important thing – plus one that directs your business into the red.
Prevention
Besides getting your return process in shape it’s important to consider unneeded comes back. The so-called NFF’s (No Fault Found comes back) cover about 68per cent of the comes back and may be paid down as well as prevented by a prevention tool in the registration of this return.
The expense of managing a return tend to be between $27 and $50, expenses which can be conserved as of this first point of contact with your buyer.
Anticipate Unexpected Pattern Times
The best reverse logistics functions are those that compress their particular cycle times at an extremely efficient level to funnel refurbished products back into the sales station. But those pattern times will not be predictable and on routine, as there are numerous facets that will throw them for a loop.
Anything from a-sharp upsurge in product demand to an extensively reported item problem or recall could turn a reverse logistics procedure that previously functioned like clockwork into one that’s facing a substantial slowdown in product reassembly or order satisfaction.
It’s important that your reverse logistics operation has actually alternative programs in place, particularly an additional warehouse or satisfaction target standby, or a customer pleasure system prepared so that you can soften any hits that customers face after an issue that causes major delays. It is important to be upcoming, help them understand the problem and something being carried out to repair it, while offering all of them a reason to stay dedicated towards brand name.
Just because your organization’s reverse logistics procedure is carrying out as in the pipeline, it is critical to keep these guidelines useful in case your business discovers it self in another of these tight spots.