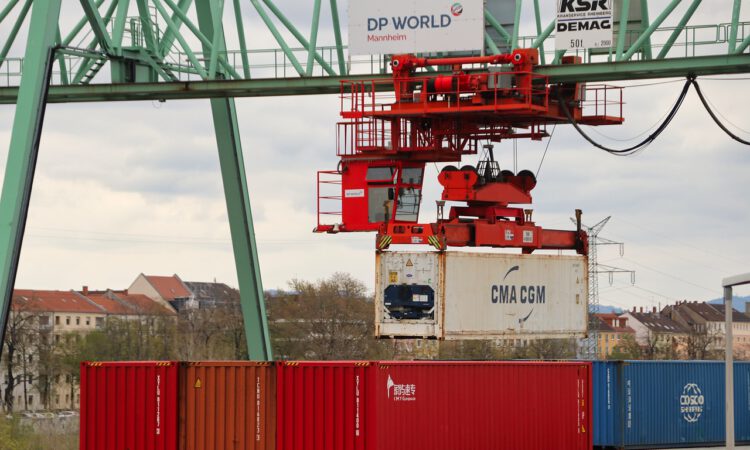
Charles Intrieri is an experienced supply chain professional and it is an accepted thought leader and innovator, mostly within the areas of supply chain optimization. Within visitor post, he shares his offer string expertise on how to operate a warehouse review and review:
Initially, glance at the stock: can it be pallets? cardboard boxes? SKUs? No, it’s cash. It’s profit a bank. The lender needs to be protected. Nobody should wander the warehouse and take components for samples/sales unless they notify the warehouse staff. Its money these are typically taking! One of several root triggers for variations in pattern relying upon turn in the warehouse versus readily available into the computer is theft!
Typically, a business’s inventory that makes up about more than half of their working capital would get a lot of attention. But actually, only a few companies appear to actually focus on their stockroom or warehouse, and/or five processes that impact it (receiving, put-away, picking, shipping and maintenance, where “maintenance” presents the mixture of cycle counting, combination, as well as other processes that retain the stockroom in great working purchase).
You can’t produce a lean warehousing procedure in the event that you don’t have efficient processes to produce products toward floor. If it will require a week or even more for inbound deliveries to go from the obtaining dock to warehouse shelves (which it several times does…) and out to the delivery home, you’re robbing various other departments (R&D, advertising, also IT) of money that could cause them to become far better.
That not enough interest presents a chance for people, which will make a positive change at their companies and consumers.
A stockroom that just keeps materials for New item Introduction will look different from a production warehouse for a tv or huge appliance factory. But with greater regularity I’ve unearthed that the difficulties I’ve observed were considering perhaps not making essential investments. Including, centered opportunities in materials dealing with businesses may have substantial ROI. Improving receiving and warehouse performance can allow you to take numerous days away from inventory.
Tips solve warehouse issues: utilize DMAIC: establish, Measure, Improve, and Control. Additionally make use of PDCA: Plan, Do, Always Check and Act. Use a cross-functional team to solve problems.
Make cycle counting and cause evaluation a central focus within warehouse: put up a large chart and post reliability percentages for all to see because inventory documents accuracy impacts ALL departments within the company.
Do you’ve got and use task interleaving within WMS? It can save you money here!
Will be your inventory switching 6-8 + times/year? Or even, it can save you money.
If you should be have automation, are you experiencing a Warehouse Control program (WCS) incorporated in to the WMS? Or do you have a Warehouse Execution program (WES=WMS + WCS)?
Exactly what defines a well-run warehouse?
Whether it’s huge or small, whether or not it manages small components, big products, or a mixture, a well-run warehouse need the next traits:
The warehouse needs a slim culture and rehearse:5S, Kaizen (and Kaizen Blitz for constant Improvement), Kanban pull methods, and slim Six Sigma. You have to continuously improve warehouse functions daily.
- In accordance with a method that is the reason the physical size of each product as well as the frequency with which it really is chosen
- SKUs may be were able to make efficient use of readily available space
- SKUs are going to be stored in an easy method that will have them safe plus in good condition – and won’t pose a risk to warehouse workers
- Products will be were able to make safe and efficient using manpower
- SKUs Slotted: Things will likely to be managed you might say to give high performance towards the warehouse’s “customer” or shipping home
- SKUs are handled in a way to attenuate control: utilization of task interleaving
- Problems and issues should be actually separated and taken care of expeditiously.
- Performance and diagnostic metrics is going to be gathered & posted.
- Obsolete, Excess and slow-moving SKUs is reviewed monthly by a cross-functional staff: Suggest disposition or modifications to administration
- Ask present staff members for his or her input to acquire buy-in
having difficulty labeling your SKUs? Decide to try our
You will find trade-offs between these, especially when sources tend to be restricted. If area is bound, a well-run warehouse should bring a few of its slow-moving components into a small area. This make picking those components less efficient, however it will raise the quantity of area (and reduce handling time) the usually selected / fast-moving components. If automation (forklifts, conveyors, etc.) is limited, the stockroom can use more floor storage space.
Other warehousing best practices
What you should see whenever walking through a stockroom and connected places like getting, staging, etc.:
- Choosing processes and storage techniques that are designed to minimize the quantity of commitment used on probably the most often selected products while keeping control of inventory. Samples of this include:
- Putting the essential frequently selected things across the primary aisle, at walk out, or close to the exit from the warehouse (toward production area). You may see, as an example, a couple of shelves with commonly picked things along the wall by the doorway; or circulation racks; if not pallets of products staged for quick distribution.
- A mixture of storage space techniques: pallet racks for things that tend to be received on pallets and are usually chosen in large volumes, movement racks, shelves for tiny components storage space, etc.
- Usage of automatic recognition tools – club rule or RFID. Without auto-ID, workers need certainly to manually keypunch deals – that will cause errors.
- Directed selecting processes, where stockroom employees utilizing RF Barcode gear are directed through stockroom in an efficient manner, in order that they choose one product, after that move to the second shelf for the next product, etc – as opposed to moving in one area to another, after that back once again to the original location.
- Cleanliness and good order: simply take turns washing the warehouse: it is your house out of the house. Use Lean’s 5S: Sort, set-in purchase, Shine, Standardize and maintain (Sustaining 5S is one of tough.) You need to be able to easily see box labels, and items should-be stacked nicely. There ought to be a clear distinction between each storage place. Typically that means a physical buffer (like a metal divider) or atmosphere. Allow it to be apparent which things come in each area. Set-up indications for: Aisles, bays, Shelves and Slots.
- Bay location IDs take the racks & racks, to spot each individual storage space location.
- Typically, one item kept per location. There may be short-term exceptions to the guideline whenever a stockroom or warehouse is near or over ability, but multiple part numbers in identical location will lead to selecting and inventory errors if allowed to be normal training.
- Focus on Safety/OSHA (main priority) and ergonomics, including sufficient and efficient lighting effects. Workers shouldn’t have to invest their times kneeling on to the floor, nor should they be asked to frequently pick up hefty containers. At least, you really need to see handbook conveyors, tables, and carts for employees to utilize while getting and picking items. If forklifts function in aisles, there must be apparent focus on protection demands. Fork Lifts should practice task interleaving so are there no “deadhead” lots into the warehouse. Each time you see a Fork Lift/Driver, they are carrying a lot, and are usually perhaps not bare.
- There should be a little holding area for obtained goods that can’t be prepared, high quality dilemmas, go back to supplier (RTV), reverse logistics and items in “quarantine” and other issue products. The things in this area should not have elderly a lot more than a week or two.
Browse Mr. Intrieri’s blog on Lean provide Chain for more information on 3PLs, warehouse administration, supply chain optimization and inventory administration and logistics. This post ended up being originally published on his blog.