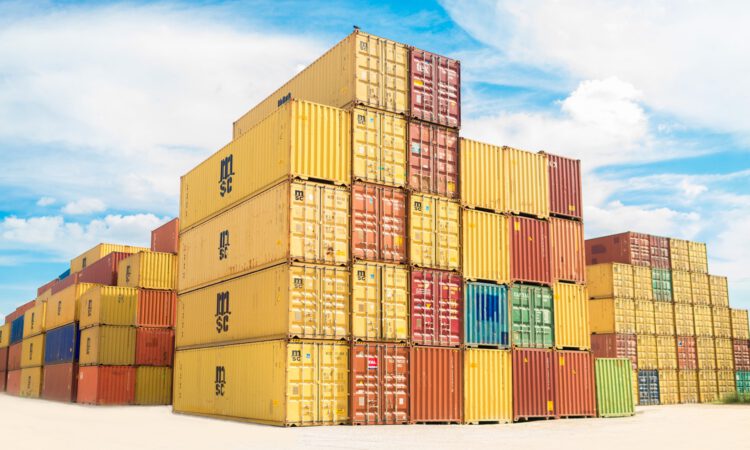
Challenge:Doing more with less in a distribution procedure by enhancing order picking productivity.
Problem? Facing level or decreasing growth prices, the pressure is on for companies to cut back running expenditures to safeguard margins.
Provide sequence executives are confronted with the process of reducing work prices, but on top of that, clients tend to be putting more requests with smaller volumes.
Clients are also under some pressure to lower expenses by lowering stock amounts and also this translates into even more expense to serve for your business.
Hence the business challenge is how-to do even more with less in the distribution operation. To the end, you will find typically opportunities to boost efficiency dependent on a business’s kick off point.
Since 50+per cent of warehouse labor resources are typically involved with choosing, packing and shipping outbound instructions, it usually makes sense to pay attention to these businesses very first.
Now may be the time and energy to revisit some standard very first axioms to maximizing warehouse effectiveness. With this entry, we focus on 5 ways to improve picking operations:
- Mixing multiple SKUs in the same container location decreases choosing productivity. We done time and movement studies that prove that there’s an absolute time penalty linked to blending numerous SKUs in to the same container location.We see this in many warehouses in which a container location may portray a rack amount which contains 5 – 10 SKU pick facings. The operator is directed into the rack level and needs to search through different SKUs to obtain the item is picked.
Not merely performs this decrease accuracy, in addition slows the operator down by as much as 15+ moments per choose exchange. Having a discrete pick location for each SKU is rule number 1.
- Decreasing vacation time gets better order choosing productivity. For this reason batch and cluster purchase choosing methods are utilized in warehouses. It’s also the reason why some businesses invest into conveyor systems.Vacation time can very quickly account for 50percent or even more of order selecting hours. By combining requests into an individual vacation instance the full time spent travelling is significantly paid off. Small the order, the greater the chance to combine several sales into a single vacation instance.
- Traditional purchase selecting efficiency improves when it’s at ground level. The statement so it costs even more to pick vertically than it will to pick horizontally is an usually acknowledged concept which has been demonstrated through benchmarking efforts over time.The truth is that some companies are lacking the actual estate at walk out to offer pick facings for all SKUs thus they have to choose vertically want it or not. Parts distribution facilities are typical for this situation. In these cases, assign the slowest velocity what to be picked from vertical locations and the keep the fastest velocity items at floor level to minimize the penalty related to vertical picking.
- Purchase selecting output improves with “hit” thickness. If an operator picks from one out of each and every 100 pick areas then this is slower than if the operator picks from a single out of every 10 pick areas. Higher pick thickness = greater choose output.Therefore it would likely sound right to setup hot zones into the warehouse to focus the SKUs that create nearly all picking activity. Some warehouse operations have ABC velocity meanings so that the quickest moving “A” SKUs sit collectively within designated broader operating aisles to lessen obstruction. By enhancing the pick thickness of the “A” items, travel time is paid down additionally the chance to increase the selecting process is greatly enhanced.
- Warehouse performance is enhanced when products are assigned towards the proper storage news. Imagine if all operators have wet paint on the arms, then optimized warehouse has got the minimal wide range of finger prints on the boxes. Each group of finger prints prices cash. Taking finger marks from the bins implies the warehouse was set-up to attenuate product maneuvering.Initial basic principle to-be followed is that things must certanly be kept in the correct storage space news. Having slow moving SKUs in pallet racks are because wasteful as having fast moving SKUs in shelving containers. We make this decision centered on a variable called cube movement velocity which steps the quantity of activity for each SKU. The cube movement velocity = motion in products x cubic measurements of device.
Measuring this metric for each SKU provides an important way to make sure that items…